工場の電気代削減を目指すあなたへ。この記事では、電気使用状況の正確な把握から始まり、電気代の算出方法、そして実際の削減策まで、効率的な電力管理の全貌が明らかになります。省エネルギーを実現するための具体的な手法と実際に成功した企業の例を通して、あなたの工場でも実行可能な対策が見つかることでしょう。
1. 工場の電気使用状況の正確な把握方法
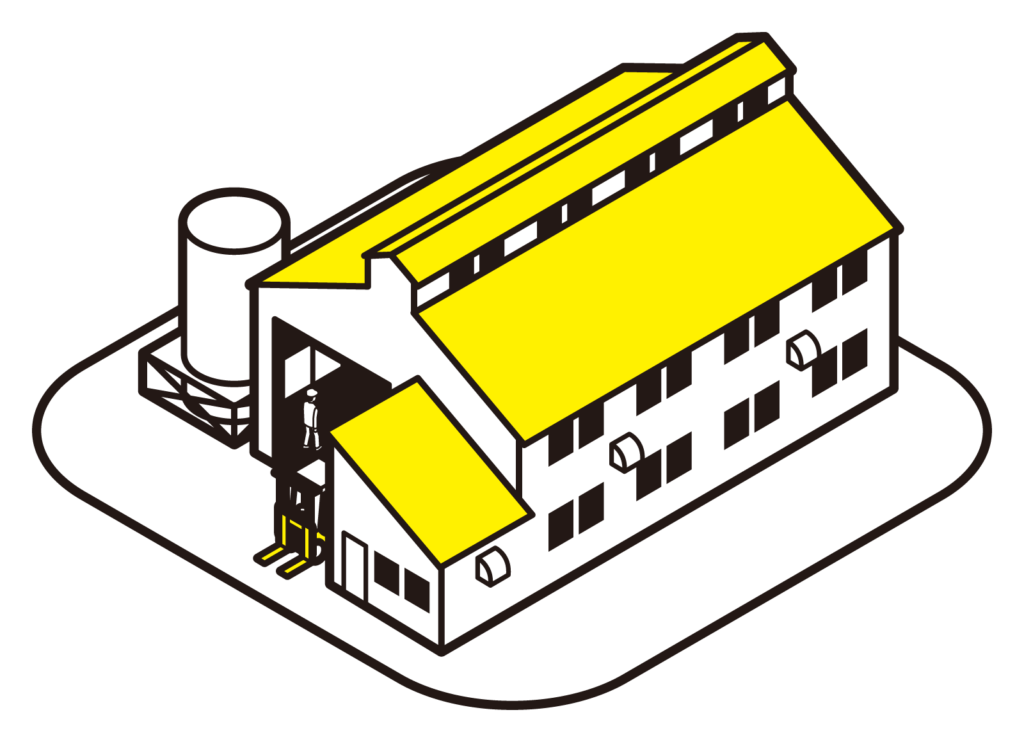
工場における電気使用状況の正確な把握は、電気代削減の第一歩です。使用量を知ることで、過剰な消費を見つけ出し、無駄を省くことが可能になります。
1.1 電気使用量のモニタリング方法
電気使用量を把握するためには、適切なモニタリングシステムの導入が必要です。市販されている電気使用量モニタリングツールを活用することで、リアルタイムでの消費状況を把握し、データを収集することができます。
1.2 電気使用パターンの分析
収集した電気使用データを分析することで、特定の時間帯における電気使用のピークや、不必要な時間帯の使用を特定することができます。この分析を通じて、効果的な節電策を立てることが可能となります。
1.3 エネルギーマネジメントシステム(EMS)の活用
エネルギーマネジメントシステム(EMS)を導入することで、より高度な電気使用状況の管理と分析が行えます。EMSは電気使用の最適化を図るための自動制御機能を有しており、消費電力の削減に大きく寄与します。
2. 電気代の算出方法
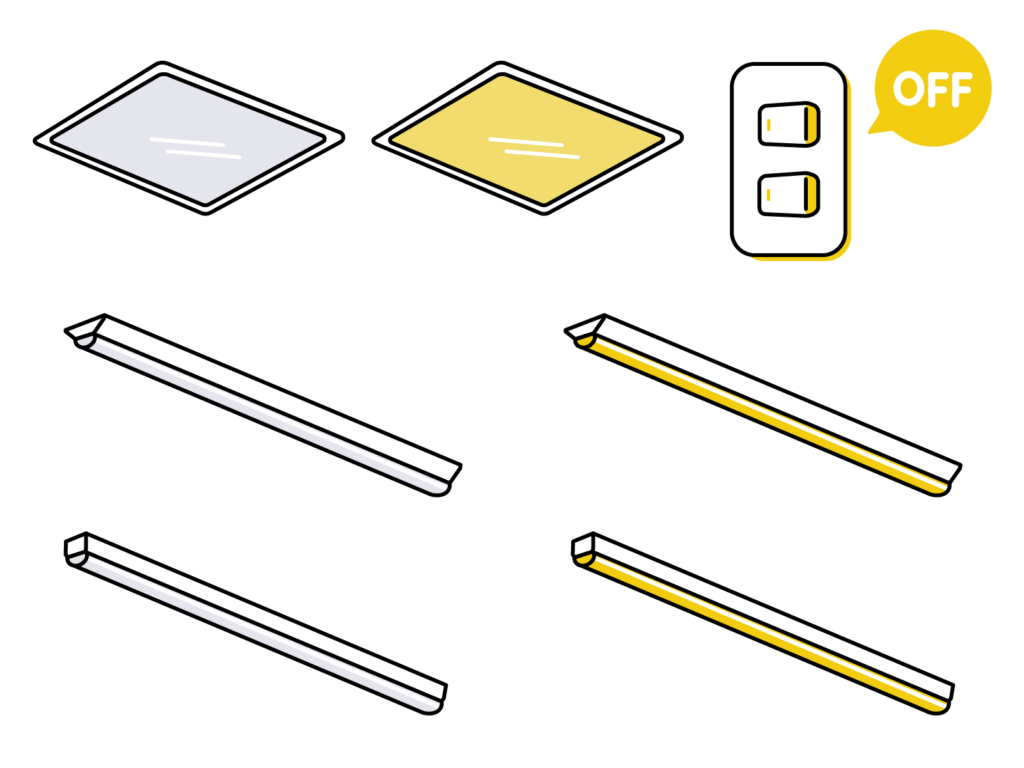
電気代を正確に算出するためには、電気料金の基本知識を身につけることが重要です。電気料金は、使用する電力の量と時間帯、さらには契約している電力会社や契約プランによって大きく異なります。ここでは、電気代を算出する際に必要な基本知識と具体的な計算方法について解説します。
2.1 電気料金の基本知識
電気料金は一般に、基本料金と従量料金から構成されます。基本料金は、契約アンペア数や器具の容量に応じて定められ、月ごとに一定額が請求されます。一方、従量料金は使用した電力量に応じて計算され、電力量が多いほど料金が高くなります。加えて、電力を使用する時間帯によっても料金が異なる場合があるため、ピーク時間帯の電力使用は料金が高くなる可能性があります。
2.2 高圧電力と低圧電力の違い
工場などの大規模な施設では、高圧電力が使用されることが一般的です。高圧電力は低圧電力に比べて送電ロスが少なく、大量の電力を効率良く使用することができます。そのため、高圧電力を利用すると電気料金が割安になる傾向にあります。しかし、高圧電力を使用するためには専用の設備や契約が必要であり、その導入コストも考慮する必要があります。
2.3 電気使用量から電気代を算出する方法
電気代の算出方法は、まず電気使用量を確認し、それを契約している電力会社の料金プランに照らし合わせて計算します。料金プランは、基本料金や従量料金に加え、時間帯別料金や季節ごとの料金変動を含むことがあります。したがって、正確な電気代を算出するには、これらの料金体系を把握し、自施設の電気使用パターンを正しく分析することが必須です。
以下に、電気代の算出例を示します。
項目 | 単価 | 使用量 | 料金 |
---|---|---|---|
基本料金 | – | – | 5,000円 |
従量料金 | 22円/kWh | 1,000kWh | 22,000円 |
時間帯別料金(ピーク) | 30円/kWh | 200kWh | 6,000円 |
この例では、基本料金に加えて従量料金、時間帯別料金を考慮した場合の電気代が合計で33,000円となります。ただし、実際の電気代は契約内容や使用状況によって異なるため、具体的な計算には契約している電力会社の料金プランを確認することが重要です。
3. 電気代削減のための対応策
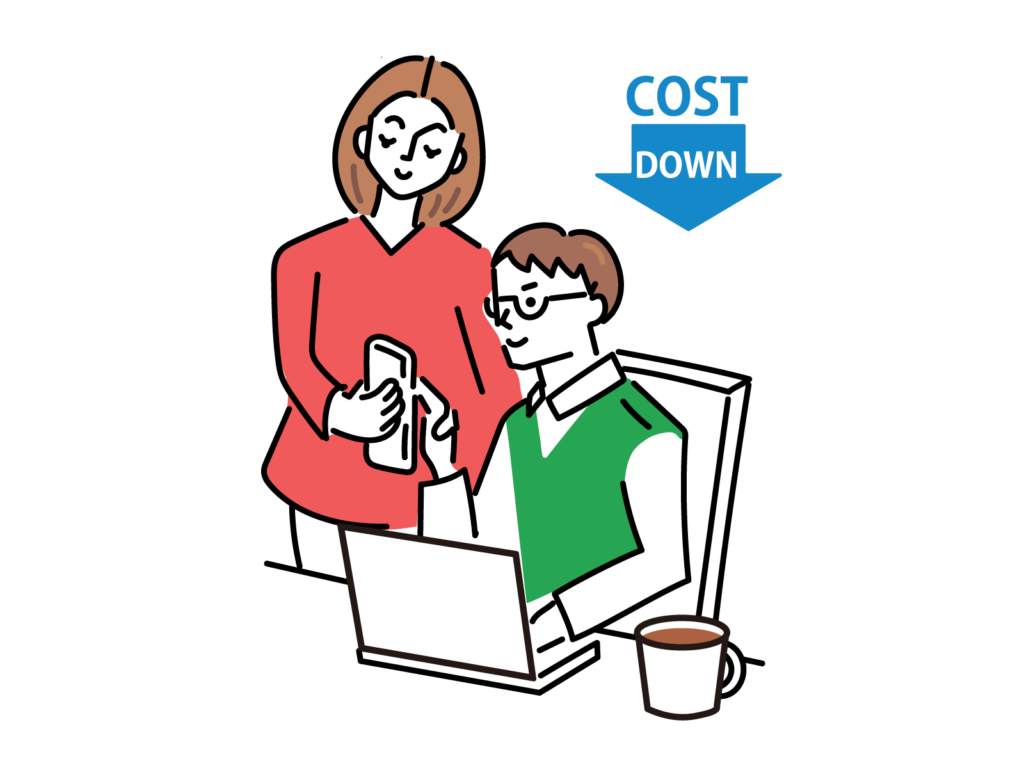
業務効率と環境への配慮の観点からも、工場の電気代削減は重要な課題です。ここでは、実際に工場で実施できる電気代削減のための具体的な対応策を紹介します。従来の設備や運用方法に見直しを加えることで、電気使用量を減らし、結果的に電気代の削減に繋がります。
3.1 照明のLED化
工場内の照明は大量の電力を消費します。特に古い型の蛍光灯や白熱灯を使用している場合、電力消費が大きい上に照明効率も低いため、効果の高い削減策の一つが照明のLED化です。LED照明に交換することで、消費電力を大幅に削減するとともに、長寿命であるため、ランニングコストの低減も見込めます。
3.2 省エネ型機器への更新
製造ラインや空調設備など、工場内で使われている機器類は電気代削減の大きなカギを握っています。これらの機器を最新の省エネ型に更新することで、消費電力の削減を図ることができます。初期投資は必要ですが、長期的な視点で見ると、大幅なコスト削減に繋がります。
3.3 運転時間の見直しと最適化
工場の機械設備の運転時間を見直し、無駄な稼働を減らすことも電気代削減に有効です。特に生産計画に基づき、必要最低限の運転にとどめる最適化を目指すことが大切です。また、ピークタイムを避けて機械を稼働させるなど、電気料金の時間帯別料金制を活用することも一つの方法です。
3.4 電力ピークカットの実施
工場全体の電力消費量がピークに達する時間帯を特定し、その時間帯における消費電力を意図的に下げることが電力ピークカットです。これにより、契約電力を超えることなく運営が可能となり、電気代の削減に大きく貢献します。運用管理の見直しや自動制御システムの導入などを通じて、電力使用のピークを抑える工夫が必要です。
4. 成功事例
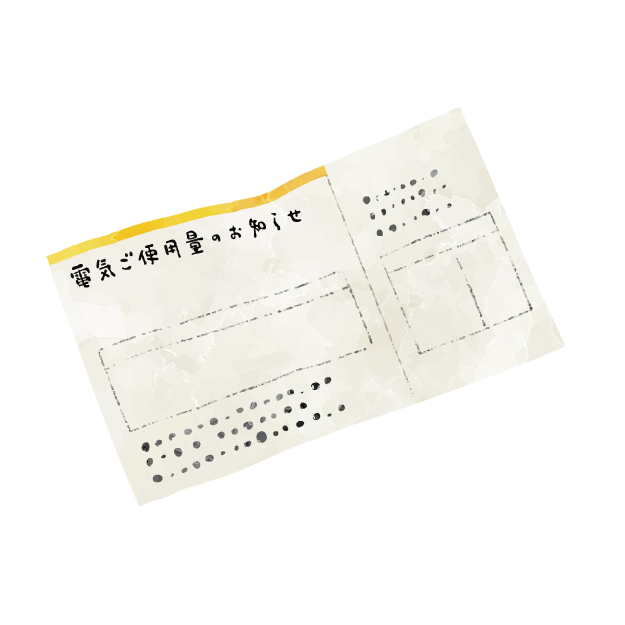
工場の電気代削減実践例を見てみましょう。具体的な対策を施した結果、どのような改善が見られたか、効果的だった電気代削減策を中心に紹介します。
4.1 導入前後の電気使用量と電気代の比較
ある工場では、電気使用量のモニタリングと省エネ対策を徹底することで、電気代に大きな差を生み出しました。具体的なデータを以下の表にまとめています。
項目 | 導入前 | 導入後 | 削減率 |
---|---|---|---|
電気使用量(kWh) | 500,000 | 350,000 | 30% |
電気代(円) | 7,500,000 | 5,250,000 | 30% |
省エネ型機器の導入やLED照明への更新、運転時間の見直し等を行った結果、電気使用量と電気代が共に30%削減されました。
4.2 効果的だった電気代削減策
- 照明のLED化: 従来の照明からLED照明に変更することで、消費電力が大幅に削減されました。
- 省エネ型機器への更新: 古い機器を最新の省エネ型に更新したことで、効率良く電力を使用することができるようになりました。
- 運転時間の見直しと最適化: 生産設備の稼働時間を見直し、無駄な稼働を削減しました。また、必要な時間にのみ機器を稼動させる運用改善を行いました。
- 電力ピークカットの実施: 電力使用量がピークに達する時間帯を分析し、その時間帯の電力使用を抑制することで、電力コストの高騰を防ぎました。
これらの対策により、顕著な電力削減を実現しました。電気代の削減は、経営全体のコスト削減にも大きく寄与します。各工場での環境に応じて適切な対策を検証・導入することが、電力コスト削減の鍵となります。
5. まとめ
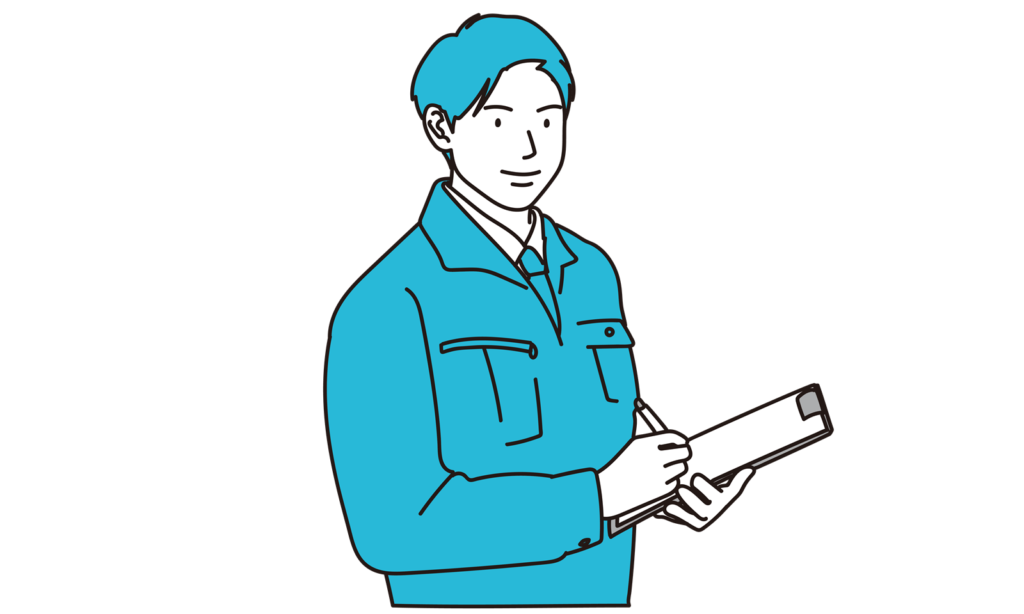
工場の電気代削減は、電気使用状況の正確な把握、電気代の算出、そして具体的な削減策の実施によって達成されます。電気使用量のモニタリング、エネルギーマネジメントシステムの活用、照明のLED化、省エネ型機器への更新、運転時間の最適化、電力ピークカットの実施など、効果的な対策を講じることで、電気使用量と電気代を大幅に削減することが可能です。成功事例を参考に、各工場が環境に応じた対策を検証・導入することが重要です。
鳥取県の中小企業様で、電気設備でお困りでしたら斉木電気設備へお知らせください
斉木電気設備では、私たちのサービスは、お客様のニーズに密着したものです。太陽光発電設備の導入から省エネ改善まで、私たち
はあらゆるニーズに対応します。私たちの目標は、最高のサービスを提供し、お客様の日々の生活やビジネスを快適で便利なものにすることです。